At VPLASMA
We excel in the creation of top-notch plastic injection molded parts and mold tools. Our expertise extends to machining and finishing services, enabling us to craft tools from a diverse range of materials. Whether you require 50 or 100,000+ finished parts, we deliver with precision and excellence in a wide array of plastics.
Backed by an international team of skilled engineers and technicians, we are committed to realizing your custom part needs using cutting-edge equipment and techniques. From Plastic Injection Moulding to CNC Machining, 3D Printing, and Vacuum Casting, we leverage the latest advancements to bring your product ideas to life. At Star Rapid, we're dedicated to transforming your concepts into tangible realities!
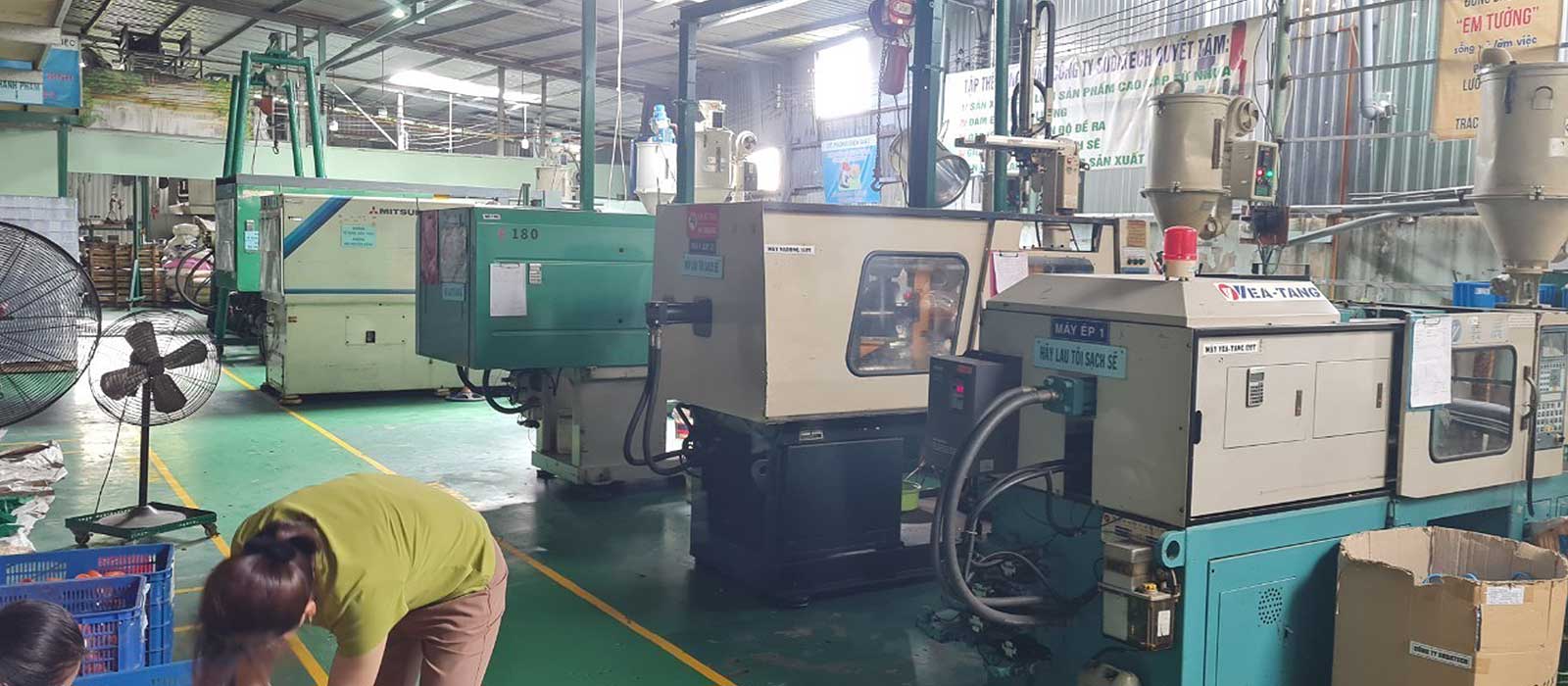
The Molding Process
Plastic injection molding is the process of filling a mold tool with liquid plastic resin under great pressure. The tool may comprise a single cavity or hundreds of cavities in order to make indefinite numbers of parts. Once the mold tools have been carefully designed and manufactured, the molding process consists of the following basic steps:
- Step 1 – The plastic resin comes in raw pellets. These are dried to the right moisture content, and then if necessary they can be blended with pigments or master batch colorants to create the correct color for the design.
- Step 2 – The dried pellets are poured into the hopper of the molding machine. A reciprocating screw inside the barrel of the machine is used to transport these pellets towards the mold while at the same time heating them.
- Step 3 – Within the barrel, the pellets are mixed and heated until fully molten, forming the liquid resin.
- Step 4 – The heated mold closes automatically and resin, under great pressure, is injected through a gate and into the mold cavity.
- Step 5 – The mold is cooled in a short amount of time to solidify the part inside.
- Step 6 – The mold opens and the part is ejected to begin a new cycle.